Detailed explanation of the molding process applied in precious metal precision casting
- Share
- publisher
- Lisa
- Issue Time
- Jul 23,2019
Summary
Detailed explanation of the molding process applied in precious metal precision casting. Yinxiao Machinery specialized in precision investment casting with various surface treatment .
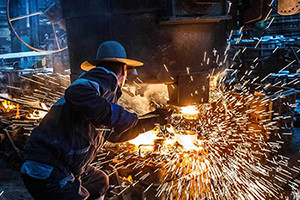
1.Definition and classification of metal casting
Definition of casting:
The liquid metal is poured into a mold cavity adapted to the shape and size of the part, and is cooled and solidified to obtain a production method of the blank or the part, which is generally called metal liquid forming or casting.
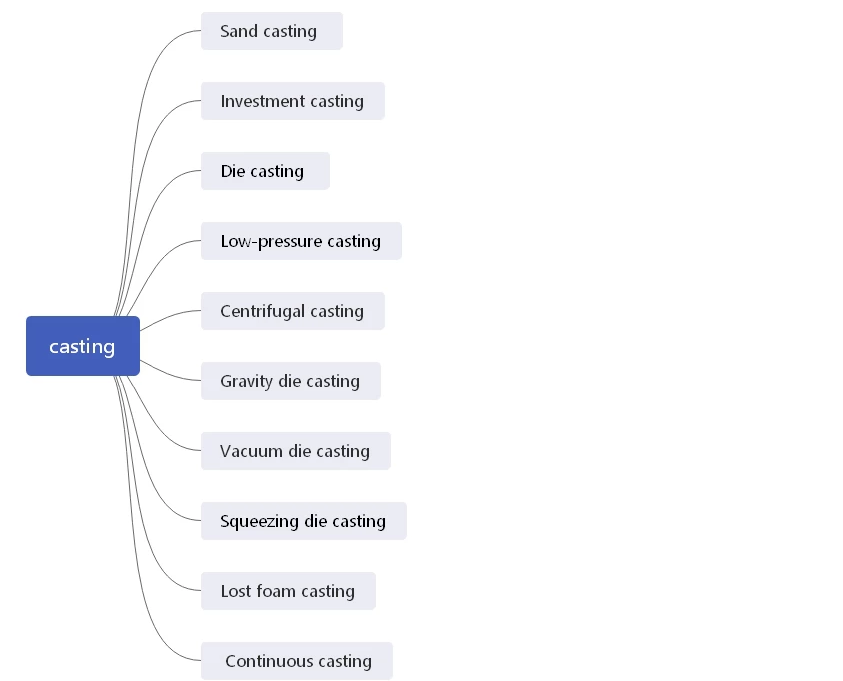
Process flow: liquid metal → filling → solidification shrinkage → casting

Sand casting:
Sand casting - a casting method for producing castings in a sand mold. Steel, iron and most non-ferrous alloy castings can be obtained by sand casting. Because the molding materials used in sand casting are cheap and easy to obtain, the castings are easy to manufacture, and can be adapted to the single-piece production, batch production and mass production of castings. For a long time, it has been the basic process in casting production.
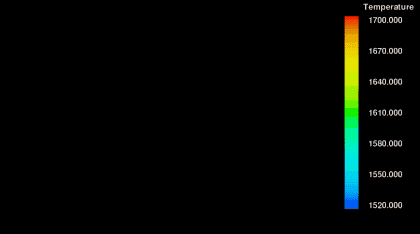
Precision casting:
Precision casting is a general term for precision casting processes using precision molding methods. Its products are precise, complex, close to the final shape of the part, can be used directly without machining or processing, and it is an advanced process of near net formation.
2.Casting process inventory for the precious metals industry
Although the inventory is divided into separate processes, due to the advantages and disadvantages of the process, there will be cross-correlation or mutual cooperation in actual production.
01.Investment casting
Investment casting, also known as "lost wax casting", refers to the process of forming a fusible material into a mold, coating the surface of the mold with a refractory material, and then melting the mold to discharge the shell to obtain an empty cavity. A casting scheme that can be cast after roasting.
The most widely used in the jewelry industry is this process. (Similar to the lost foam casting process, the difference is that the investment casting is to melt the mold to form a cavity before casting, and the lost foam casting is to directly mold the molding cavity in the casting, which is not conducive to the processing of complex workpieces).
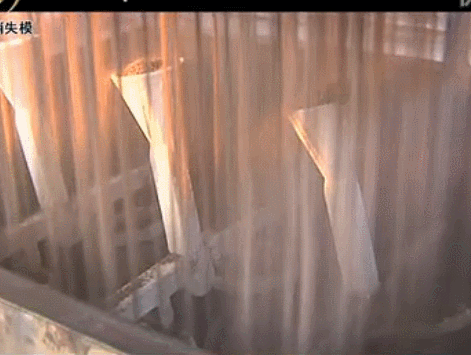
Vanishing mold casting process
Jewelry industry application process:
starting version - trimming wax mold (welding wax mold) - kind of wax tree (-weighing) - filling gypsum tube - gypsum vacuum - gypsum natural solidification - baking gypsum - Melting gold, casting.
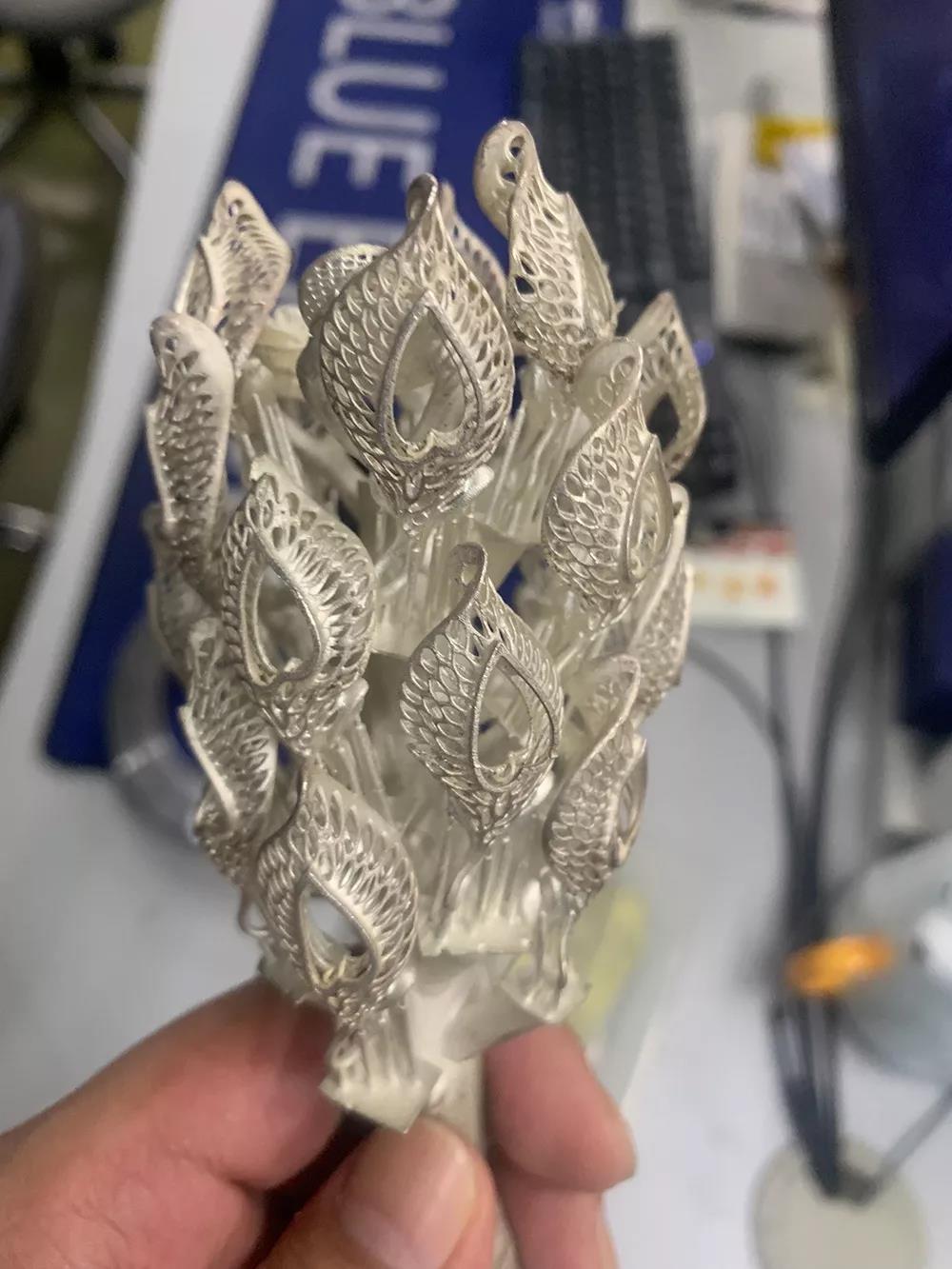
Advantage:
1. High dimensional accuracy and geometric accuracy;
2. High surface finish;
3, capable of casting complex castings.
02 Pressure casting
Uses high pressure to press the molten metal into a precision metal mold cavity at high speed, and the molten metal is cooled and solidified under pressure to form a casting.
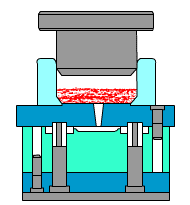
Advantage:
1. The metal liquid is subjected to high pressure and fast flow rate during die casting;
2, the product quality is good, the size is stable, and the interchangeability is good;
3, high production efficiency, the number of times the die-casting mold is used;
4, suitable for mass production.
The jewellery industry often uses this casting process to work with vacuum and inert gas to prevent oxidation.
Unique stirring induction heating, working with vacuum pressure gravity casting principle; precise digital temperature control system, temperature control error is controlled at ±2 °C; vacuum and gas protection melting to ensure metal gasification to the lowest point, pressurization The funnel type blanking material ensures that the workpiece is injected into the mold at the fastest and best condition, the reduction performance is good, the casting has high success rate, high density and good surface finish, and the basic non-shrinkage casting is achieved.
03 Vacuum casting
It is a process that uses a ventilated mold. The molten metal flows into the mold by air pressure and then removes the air to form a vacuum. This casting method is mainly used for small parts or jewelry with intricate details.
The jewellery industry uses this process in a wide range of vacuum suction molding and vacuum differential pressure casting.
1. Vacuum suction casting
The mold is placed in a closed container, and the air in the mold is extracted to cause a certain negative pressure in the mold, thereby causing the molten metal to be sucked into the cavity. When the inner runner of the casting solidifies, the negative pressure is removed.
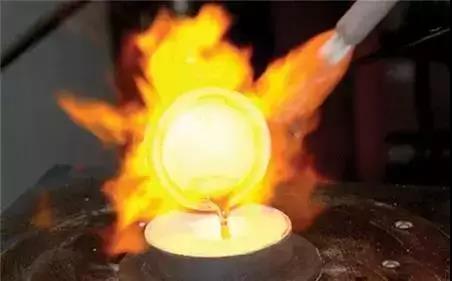
2, vacuum differential pressure casting
Vacuum differential pressure casting mainly seals the electric resistance holding furnace and the mold, and introduces a compressed air with a large pressure in the sealing cover, and then replenishes the pressure on the molten metal surface, and the molten metal fills the cavity. Especially suitable for the production of complex thin-walled castings.
The advantages are as follows:
(1) Compared with traditional gravity casting and vacuum suction casting, vacuum differential pressure casting has a good filling ability on a thin wall.
(2) Castings have denser crystal structure and mechanical properties, which are improved in strength and performance of castings compared to vacuum suction casting and gravity casting.
(3) Vacuum die casting can effectively reduce the pores of the die-casting parts and increase the density of the castings.
04 Centrifugal casting
Centrifugal casting is a technique and method for injecting liquid metal into a mold that rotates at a high speed to fill the mold and form a casting under the action of centrifugal force.
The characteristic of centrifugal casting is that the molten metal is filled and solidified under the action of centrifugal force, the metal feeding effect is good, the outer layer of the casting is dense, and the non-metallic inclusions are few.
Centrifugal casting can obtain castings without shrinkage, pores and slag inclusion, and has fine structure and good mechanical properties. However, centrifugal casting is not suitable for casting alloys which are prone to specific gravity segregation.
It should be noted that the number of revolutions of the mold is an important parameter for centrifugal casting. It is necessary to have sufficient centrifugal force to increase the compactness of the casting metal, but the centrifugal force cannot be too large to prevent the metal from shrinking.
Centrifugal casting machine is widely used in the jewelry industry for casting platinum group metals (poor flow and fast cooling)
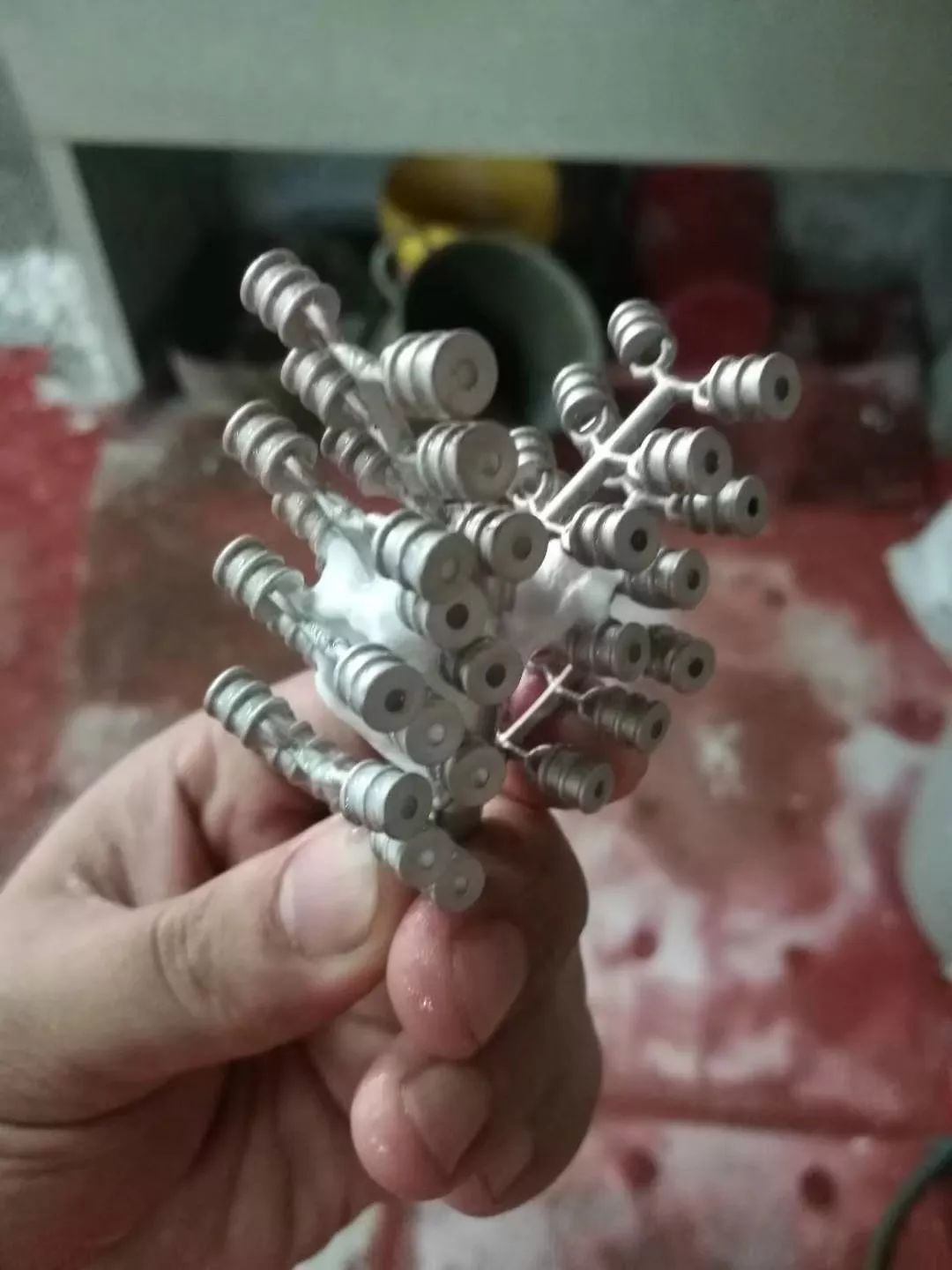
05 Continuous casting
It is an advanced casting method. The principle is that the molten metal is continuously poured into a special metal type called a crystallizer. The solidified casting is continuously pulled out from the other end of the crystallizer. Castings of any length or length.
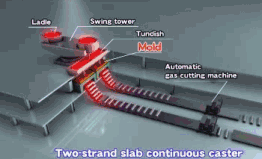
Advantage:
1. Since the metal is rapidly cooled, the crystal is dense, the structure is uniform, and the mechanical properties are good;
2. During continuous casting, there is no riser of the casting system on the casting (similar to the external nozzle on the wax part when the mold is poured), so the continuous ingot does not need to be cut and tailed during rolling, which saves metal and improves the yield. ;
3. Simplified the process, eliminating the shape and other processes, thus reducing the labor intensity; the required production area is also greatly reduced;
4. Continuous casting production is easy to realize mechanization and automation, realize continuous casting and rolling, and greatly improve production efficiency.